Extreme testing parameters of quaternary ammonium salts on contract seating fabric drives need for super high-performance lacquers.
The Quat Compound
Upholstery fabric used in the contract seating market in mass transit, medical, and hospitality applications can breed harmful bacteria with widespread capability. Since the pandemic has swept the world, cleaning and disinfecting commonly touched surfaces have become more frequent and thorough, and rightfully so.
Quaternary ammonium chloride compounds, often referred to as “quats” or QACs, have been widely used for decades as the active ingredient in disinfectants. QACs are exceptionally effective in eliminating germs by absorbing into the cell walls of bacteria, damaging the membrane, and killing the bacteria. One of its pitfalls, however, is damaging the lacquer as well as the printed pattern on the vinyl fabric. After the lacquer is compromised, QACs will damage the substrate. With more frequent exposure and concentrated disinfectant formulas, vinyl upholstery is forced to withstand conditions for which it was not intended.
When developing new OEM lacquer chemistries for flexible vinyl upholstery fabric, it is important to know the experimental coating’s response to extreme exposure to quats. APV employs various industry standard methods for testing coating performance on upholstery fabrics, including CFFA-Heathcare 201 (Chemical Fabrics and Film Association Inc.) and BIFMA HCF 8.1-2017 Health Care Furniture Design Guidelines for Cleanability. There are also modified ways for testing cleanability and chemical resistance with more severe conditions that have evolved since COVID-19. This was due to new disinfectant types and enhanced cleaning protocol for hospitality and healthcare industries.
The Hot Seat
Once passing BIFMA and CFFA standards, APV takes quats to the hot seat. The most severe modified experiment APV uses involves fifteen consecutive days of testing in a hot oven.
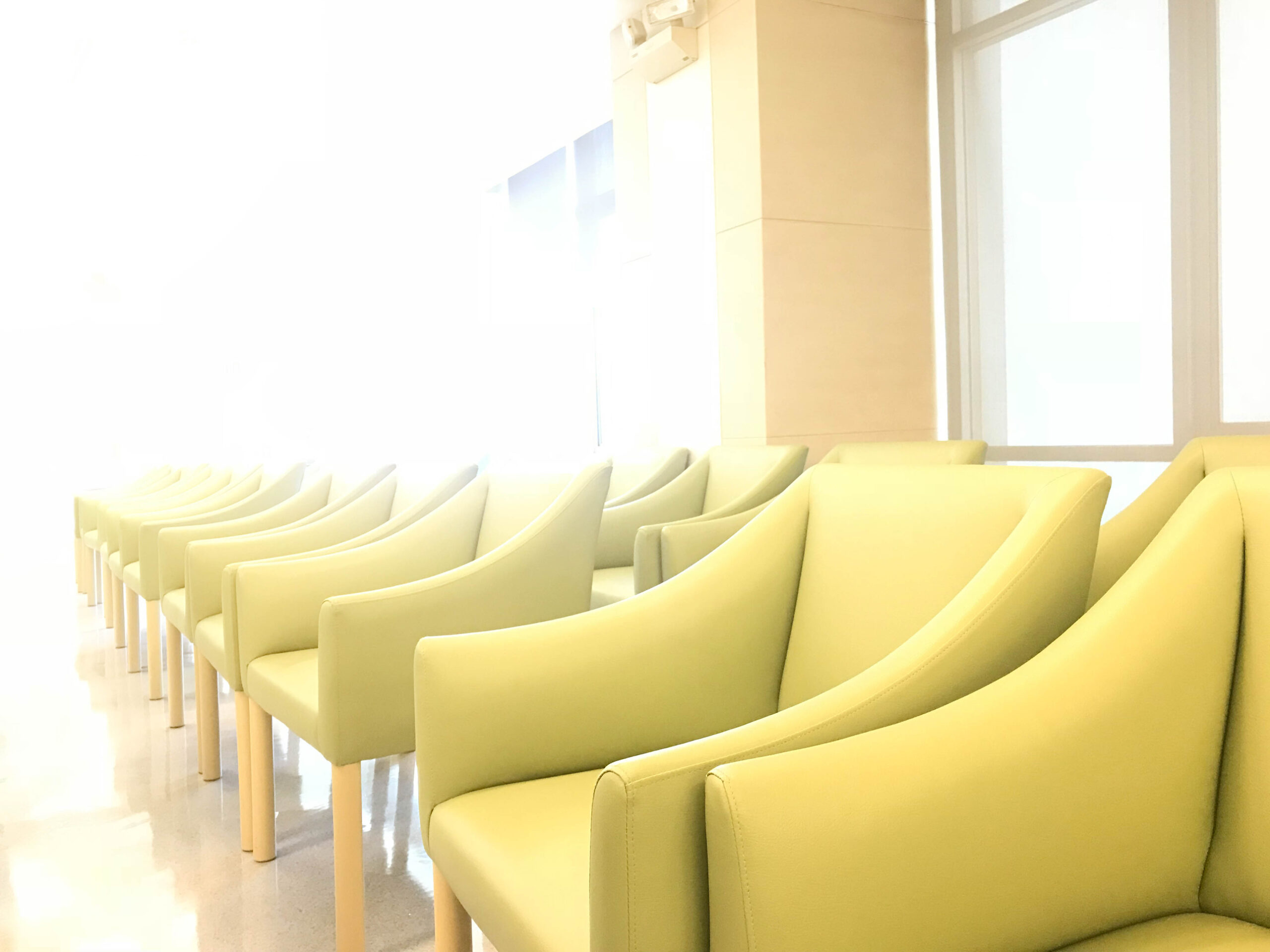
To start this test, a quat cleaner of a specific dilution is wiped onto two samples of printed and lacquered upholstery fabric, just as if you were cleaning the surface. Both samples are then placed into an oven at 70˚ C (158˚ F). Each day, the samples are removed, wiped with cleaner, and put back into the oven. On the first sample, the cleaner is applied to the surface, then removed by wiping with water. On the second sample, the cleaner is applied to the surface without further action.
After fifteen days of the same process, the samples are evaluated for changes in color, gloss, haptics, flexibility, and hardness against the standard ASTM D-2240. Sometimes, the tested samples receive additional abrasion testing following ASTM D-4157 Standard Test Method for Abrasion Resistance of Textile Fabrics.
Optimizing the Performance of Upholstery
These robust testing procedures, require new coating technologies with extreme chemical resistance. When formulating, it is essential to collaborate with raw material manufacturers to engineer unique polymer binder systems with increased functionality. It is then imperative to leverage this binder, the chemical backbone of the coating, to increase crosslink density with the use of different types of isocyanates and carbodiimides. Once the formulation of coating is constructed and thoroughly tested, it is important to collaborate with vinyl manufacturers to ensure efficiency in largescale application processes without compromising the most important quality, performance.