A Quick Guide on Steel Substrates and Surface Prep
Download the Free White Paper
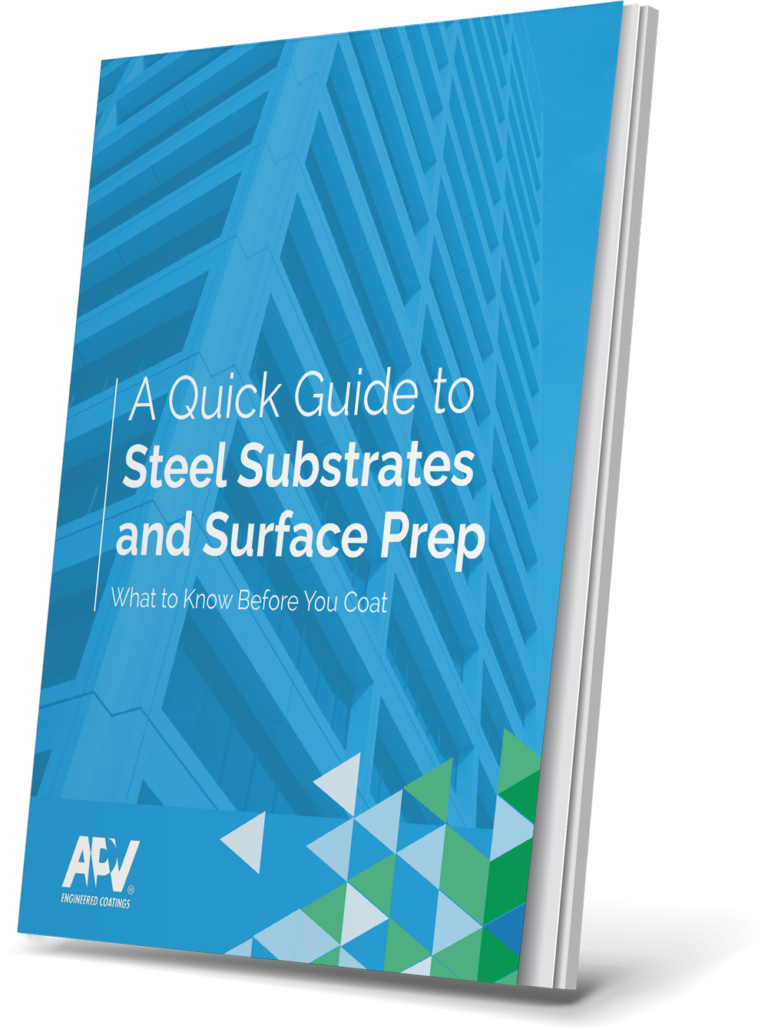
The Importance of Preparation in Exterior Coating Projects
Exterior coating restoration projects involving architectural steel surfaces should always include a case-by-case inspection to identify the proper preparation and products needed to ensure optimum protection. From the environmental conditions of the building to the current condition and type of steel to the type of coating system specified, several important details can affect the short- and long-term success of coating a steel exterior.
Download this white paper to learn more about:
- The 4 C’s of Surface Preparation
- Climate
- Corrosion
- Condition/Cleanliness
- Coating
- Overcoating vs. Removal
- Priming
- Intercoat Adhesion
- Benefits of PVDF-Based Coatings